Warehouse Rack Collapse: Causes and Preventive Measures
Generally, warehouse pallet racks possess a robust construction. It is designed to withstand an enormous load. It certainly makes an impact on the whole inventory management. An organized warehouse rack makes a huge impact on operational productivity. However, sometimes we hear some accidental cases of warehouse racking collapse. Isn’t it unusual for a robust rack to collapse? Well, of course, it is. Warehouse pallet racks don’t just collapse. There has to be a concrete cause behind this massive failure. This post focuses on the causes of racking collapse in warehouse. Let us discuss what makes immediate or long term failure of pallet rack in the warehouse.
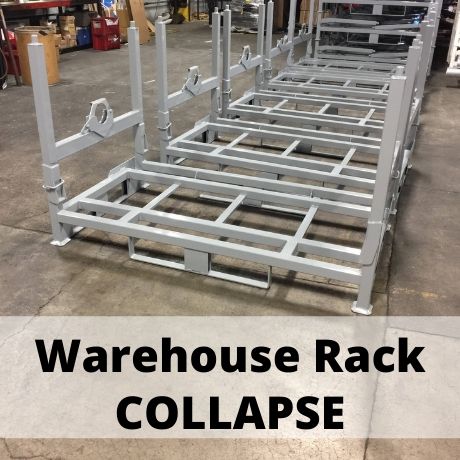
What are the Main Causes of Pallet Rack Collapse?
A pallet rack may damage due to several reasons. The below section analyzes them in detail.
- Forklift Damage: The forklifts are of great help in the warehouses, as they can literally lift heavyweights, which are not possible for workers to carry. These forklifts are automized, still, they can be one of the causes of warehouse rack accidents. At times, this equipment may not function as expected and sometimes may damage while in action. If a forklift becomes uncontrollable due to some internal damages, then it can crash into pallet racks thereby causing racking collapse in warehouse.
- Installation Errors: A warehouse pallet rack installation is a complex process. Even though the racks look like just stacked up pallets and shelves, its installation requires planning. There are many components that are installed in a rack system for stability and safety purposes. A well-designed racking system can collapse if not installed and maintained well. Wrong part attachment, loose-fitting, etc can cause warehouse racking collapses.
- Design Deficiencies: Many warehouse racks are custom designed because all standard racks may or may not be suitable for specific requirements. A warehouse pallet rack design takes plenty of static and dynamic force calculations such as operational loading stress, rack sustainability, forklift travel distance and speed calculations, etc. If any of the design factors are overlooked or implemented faultily, then design deficiencies can cause sudden rack collapses.
- Uneven Loading: Uneven loading in the warehouse racks can cause accidental damage. Generally, rack edges are welded and fabricated therefore are weak at the joints. Uneven load distribution can cause the stress-induced failure of certain sections of the racks.
- Beams and Uprights Overloading: The warehouse racks are exposed to vertical, as well as horizontal loading stresses. Horizontal stress is distributed over beams where the vertical force is distributed over the uprights. Both beams and uprights are designed for specific bending stress, therefore overloading causes bending and breaking of these elements. Fortunately, the failure due to beam and upright overloading is a long foreseen one. Therefore, in the primary symptoms of bending, overloading can be stopped and this damage can be prevented.
These warehouse rack collapses are often sudden yet that doesn’t mean they cannot be prevented. Let us discuss a few preventive measures for warehouse rack and pallet safety.
How to Prevent a Pallet Rack Collapse?
The following are some tried and tested ways to prevent pallet rack failures.
- Installation of Rack Protection: A small investment in-rack protection installation can help avoid sudden warehouse rack collapse. The fact that a pallet rack system has multiple moving components and operators being humans cannot be 100% vigilant, make it susceptible to sudden hit and fall accidents. Therefore, to prevent such failures, rack protection installation like end-of-aisle and aisle-column protection must be installed.
- Ensure Aisle Clearance and Visibility: Many warehouse accidents are caused due to obstacles and cluttered racks. Therefore, you must consider spacious aisle clearance during the warehouse rack design itself. It clears a path for operation and halts while increasing visibility.
- Decrease Speed Limits: High-speed forklift operations cause serious accidents. To prevent this, there must a safe speed limitation.
- Conduct Operator Training: Inexperienced operators are prone to panic and make mistakes. Therefore, train your operators before handing over the controls. It surely can reduce human errors in the process.
Implementing Safety Culture in the Warehouse
Warehouse safety is of paramount importance, especially in preventing incidents like warehouse racking collapses. Establishing a safety culture within the warehouse involves fostering a collective mindset that prioritizes the well-being of employees and the integrity of storage systems. To achieve this, several key factors play a crucial role:
Promoting Safety Culture:
Management plays a central role in promoting a safety-first culture in the warehouse. They must actively demonstrate their commitment to safety by providing the necessary resources, training and support to ensure that safety protocols are effectively implemented. By setting clear safety objectives and leading by example, management sets the tone for the entire workforce to embrace safety as a top priority.
Reporting and Transparency on Potential Safety Hazards:
Encouraging employees to report potential safety hazards is vital in preventing incidents, including racking collapse in warehouse. Employees should feel comfortable speaking up about any safety concerns they identify in the warehouse, be it related to storage systems, equipment, or operational processes. Creating an environment where reporting safety hazards is actively encouraged, empowers employees to take an active role in ensuring their own safety and that of their colleagues.
Recognizing and Rewarding Safety-Conscious Behavior:
Employees who consistently adhere to safety protocols, contribute to identifying safety hazards and actively participate in safety training should be acknowledged and commended. By celebrating safety-conscious behavior, warehouses foster a positive safety culture, motivating employees to continue prioritizing safety in all aspects of their work.
Now, that the causes of pallet collapse and its preventions are well-stated, it is important to consider efficient design and installation along with the rack quality. At SPS Ideal Solutions, we provide customized steel shipping racks, that double as warehouse pallet rack systems for almost all industrial requirements. Our technical experts would work with you to understand your requirements before building the racks. This helps ensure the safety and productivity of racks.
Related Posts:
- 5 Simple Tips to Prevent Industrial Rack Damage
- How Racks Contribute in Warehouse Organization
- Top 5 Essential Tips to Minimize Warehousing Cost
- How to Solve Most Common Warehouse Management Challenges
About The Author