Most Common Warehouse Catastrophe and Ways to Avoid Them
Among the potential safety hazards in warehouses or distribution centers – with forklifts lifting and lowering heavy loads, maneuvering backward and forward – one thing that often gets overlooked is the safety of storage racks. Although it is not always the case, pallet rack failure can happen due to forklift operating errors and risky racking. Most of the time, operators negotiate tight turns in and out of the aisles. This may result in occasional accidents. That’s why it is important to draw attention to warehouse safety. If the storage racking system is not structurally sound or excessively loaded, then it may cause damage to employees as well as property. This post discusses a few easy-to-follow and proven prevention tips regarding warehouse safety procedures. Read on to know more.
5 Causes of Warehouse Catastrophes and How to Prevent Them
The following are some common warehouse incidents and prevention tips for warehouse safety. These tips are applicable in case of your existing system safety checks, storage expansion or renovation, and shifting into a new warehouse with the existing racking system.
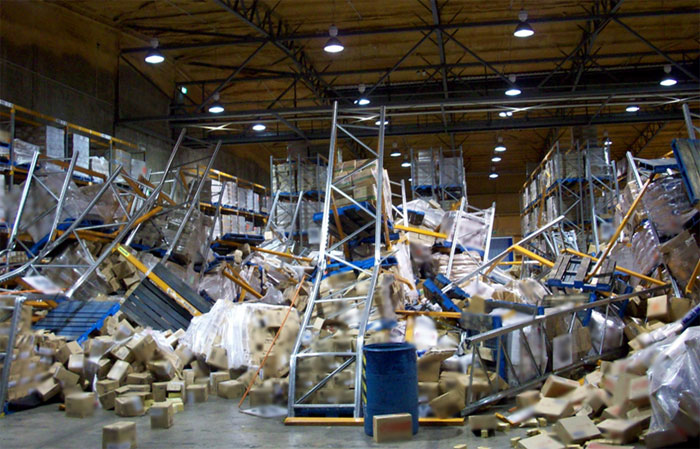
Forklift Disasters
Forklift accidents mainly occur in the corners of warehouses, intersections, and blind areas. These may lead to equipment damage, financial loss, unplanned downtime, worker injuries, and many more. According to Occupational Safety and Health Administration or OSHA, serious and fatal accidents occur when workers become complacent and comfortable while handling large and heavy pieces of equipment.
Installing an alert system is one effective way to prevent these sudden crashes. The system should caution the forklift operator whenever another person or machine is nearby. It also allows the driver to minimize the speed or maneuver in time. With safe working practices, the system reduces crashes and accidents because of forklifts.
Slips and Trips
A simple slip of the object on the warehouse floor can cause huge damage to the property. Slips, trips, and falls create a majority of accidents. This common cause of damage is preventable in many cases by keeping aisles organized, cleaning up liquid spills, unloading new products on shelves, keeping non-essential things away, illuminating darker areas, and many more.
Falling Objects
One of the effective ways to utilize the warehouse space is stacking products vertically. But, it creates the risk of objects falling down if not stored properly. Therefore, regardless of your warehouse space, it’s important to stack them the smart way. When it comes to stacking products, pay more attention to cylindrical and odd-shaped parts that could easily roll off the shelf, and cause serious damage to employees.
Ergonomic Injuries
In a warehouse, ergonomic strains are caused by several reasons such as ergonomic risk factors, exposure to abnormal temperature, and many more. To avoid this, employees should have knowledge as well as a sense of awareness for protecting themselves. Being an employer, don’t ask your employees to push their limits of what they feel they’re capable of as that invites the risk of injury. Providing proper training to all employees is essential.
Toxic and Harmful Substances
Many times, warehouse accidents may be caused by harmful substances such as acids, solvents, disinfectants, pesticides, and many more. Therefore, it is important that all employees should have protective gear like hand gloves, masks, and more. Also, rooms, where these substances are being stored, must be well ventilated.
Implementing the aforementioned tips with careful planning will help in preventing warehouse disasters, and also allow you to minimize unwanted expenses and risk of life. Are you still concerned about pallet rack safety hazards? If yes, then you must take assistance from an industry-leading storage solution supplier like SPS Ideal Solutions. The company is a one-stop solution for storage racks. With years of experience, the company prides itself on offering custom storage solutions for its clients at reasonable prices.
Frequently Asked Questions
What are the leading causes of pallet racking failure in warehouses?
Pallet racking collapse can be caused by a variety of circumstances, including forklift operator errors, shelf overload, and structural deficiencies in the racking system. To avoid such events, maintain correct installation, regular inspections, and adherence to weight capacity limitations.
How can firms reduce the danger of warehouse disasters?
Warehouse disasters, such as pallet racking collapses and forklift accidents, can have serious effects for both workers and property. Proactive safety measures, such as installing forklift alarm systems, conducting frequent safety inspections, and offering comprehensive personnel training, can considerably reduce the chance of disaster.
What precautions can be taken to prevent forklift disasters in warehouses?
Forklift disasters, like as collisions and equipment damage, are widespread in warehouse settings. Implementing safety measures such as alarm systems to warn forklift operators of surrounding impediments, providing sufficient operator training, and enforcing safe operating procedures will help prevent such mishaps and protect both personnel and equipment.
How can firms prevent warehouse shelves collapse?
Warehouse shelves collapse happens due to poor stacking procedures, overload, or structural flaws in the shelving system. To avoid such calamities, organizations should prioritize correct stacking practices, inspect shelving on a regular basis for indicators of wear or deterioration, and make sure shelves are not overloaded over their weight capacity limitations.
Related Posts:
- Guide to Warehouse Rack Labeling System
- How to Design your Warehouse Racking Layout for Optimization?
- How to Solve Most Common Warehouse Management Challenges?
- Warehouse Rack Collapse: Causes and Preventive Measures
About The Author