Warehouse Relocation Checklist: Key Tips for Moving Your Warehouse
In the intricate web of modern business operations, the relocation of a warehouse holds a significance that reverberates far beyond mere logistics. As enterprises grow, adapt, or seek to optimize their supply chains, the decision to relocate a warehouse becomes a strategic maneuver with profound implications. The very heartbeat of commerce pulses through these storage hubs, making their relocation a venture of paramount importance. However, the success of such an endeavour is not merely a result of moving boxes and equipment—it hinges on meticulous planning, foresight, and precise execution.
Warehouse relocation is a complex process that requires meticulous planning and execution to ensure minimal disruption to operations. Whether you’re moving to a larger facility to accommodate growth or relocating to a more strategic location, proper planning is essential to a successful transition. Let’s outline a warehouse relocation checklist comprising key tips and considerations to help streamline the moving process and mitigate potential challenges.
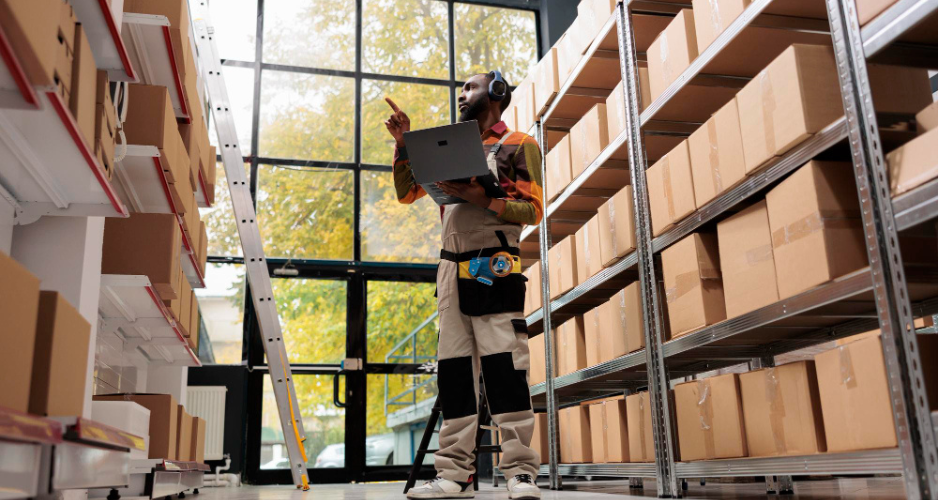
Advantages of Creating a Warehouse Moving Checklist
Implementing a comprehensive warehouse moving checklist offers numerous benefits that can streamline the relocation process and enhance the overall efficiency and effectiveness of your operations. Let’s explore some of the key advantages in detail:
Organization and Clarity: A structured warehouse moving checklist provides a clear roadmap for the entire relocation process, outlining specific tasks, timelines, and responsibilities. By breaking down the complex moving process into manageable steps, you can ensure that nothing is overlooked or forgotten, leading to a more organized and efficient relocation.
Efficient Resource Allocation: With a detailed plan in place, you can allocate resources such as manpower, equipment, and budget more effectively. By identifying the specific requirements and dependencies of each task, you can avoid duplication of efforts and optimize resource utilization to minimize costs and maximize productivity.
Risk Mitigation: Moving a warehouse involves various risks, including damage to inventory, equipment malfunction, and operational disruptions. By proactively identifying potential risks and implementing preventive measures, such as proper packing techniques, safety protocols, and insurance coverage, you can minimize the likelihood of costly setbacks and mitigate the impact of unforeseen challenges.
Minimized Downtime: Downtime during warehouse relocation can have a significant impact on productivity, customer satisfaction, and revenue generation. By carefully planning the sequence of tasks and coordinating with all stakeholders, you can minimize downtime and ensure a smooth transition to the new location. Timely communication with employees, suppliers, and customers can also help manage expectations and mitigate the impact of disruptions.
Improved Inventory Management: Relocating a warehouse presents an opportunity to reevaluate and optimize inventory management practices. By conducting a thorough inventory assessment and implementing efficient storage and labeling systems, you can enhance inventory visibility, accuracy, and accessibility at the new location. This can lead to faster order fulfillment, reduced stockouts, and improved overall operational efficiency.
Key Planning Steps for Warehouse Moving
Embarking on a warehouse relocation demands a comprehensive approach that spans critical phases to ensure a seamless transition. Here’s a preview of the essential warehouse moving steps that will guide you through each stage:
Pre-Planning Phase
Assessing the Need for Relocation: Warehouse relocation is a significant decision driven by a variety of factors that impact business operations and growth. Several triggers prompt companies to consider moving their warehouse location. As businesses expand, they often outgrow their current warehouse space. Overcrowded facilities can lead to inefficiencies, hinder workflow and compromise safety.
Companies experiencing increased demand for their products require larger storage capacities to accommodate growing inventory levels. Guidance on evaluating the need for warehouse relocation involves a thorough analysis of current and projected needs, costs, benefits and potential risks. Consider factors like inventory growth rates, customer demand patterns and the feasibility of expanding the current facility.
Setting Clear Objectives and Goals: Clear objectives are the compass that guides a successful warehouse relocation. Without well-defined goals, the process can become unfocused and susceptible to unexpected challenges. Clearly articulate what you aim to achieve through the relocation.
Objectives could include expanding capacity, improving operational efficiency, or better aligning with customer demand. Ensure that your relocation objectives align seamlessly with your business’s overall strategy and long-term growth plans. The move should contribute to achieving broader organizational goals.
Planning and Organization
Assembling a Relocation Team: Gathering a skilled relocation team is paramount. This team should comprise individuals with diverse expertise, including project managers, logistics specialists, IT professionals and representatives from different departments. Effective communication and collaboration among team members ensure a cohesive approach to the relocation process.
Budgeting and Resource Allocation: Creating a comprehensive budget is essential to prevent financial surprises during the relocation. Consider all aspects of the move, including transportation, equipment, labor and unforeseen expenses. By managing resources judiciously, you can ensure that the relocation stays on track without exceeding budgetary limits.
Timelines and Deadlines: Establishing a well-structured timeline is crucial to prevent disruptions and keep the relocation process on schedule. Break down the entire process into phases, assigning specific timeframes for each. Additionally, set clear deadlines and milestones for key tasks. Adhering to these timelines ensures that the relocation progresses smoothly and minimizes the impact on ongoing business operations.
Physical Relocation Process
Inventory Assessment and Management: Before moving, conduct a comprehensive assessment of your inventory. Categorize items based on their importance, usage frequency and condition. Identify items that may require special handling or storage conditions. This assessment helps you determine what to relocate, what to dispose of, and what to sell.
Selecting a New Location: Choosing the right new warehouse location is a critical decision. Consider factors like proximity to suppliers, customers and transportation hubs. Assess the availability of necessary amenities, local regulations and potential expansion opportunities. The new location should align with your business’s strategic goals and facilitate efficient distribution and operational processes.
Logistics and Transportation: Coordinating logistics and transportation is key to a successful relocation. Select reliable transportation providers that can handle your inventory’s volume and specifications. Plan the transportation routes, considering factors like distance, traffic conditions and potential detours. Properly pack and secure items for transit to minimize the risk of damage during transportation.
Post-Relocation Phase
Unpacking and Setup: After physically moving to the new warehouse, the unpacking and setup phase begins. Efficiently organizing and arranging items like racks in their designated places is essential. Unpack systematically, prioritizing items based on their immediate need and usage frequency. Ensure that the layout is optimized for workflow efficiency, enabling seamless operations from the moment the doors open.
Testing and Quality Assurance: Upon setting up, thorough testing and quality assurance procedures are imperative. Test all equipment such as pallets, systems and technology to ensure they are functioning as expected. Rigorous quality assurance checks guarantee that your warehouse’s systems are operating optimally and that any potential problems are identified and resolved before they escalate.
Things to Consider Before Making a Warehouse Move Checklist
Before creating a warehouse relocation checklist, it’s essential to consider several key factors that can significantly impact the warehouse moving. By addressing these considerations upfront, you can develop a comprehensive warehouse move checklist that addresses your specific needs and ensures a smooth and successful move. Here are some important things to consider:
Business Objectives and Requirements: Start by clarifying the overarching objectives and requirements driving the warehouse relocation. Whether it’s expanding capacity, improving operational efficiency, or reducing costs, understanding your business goals will help prioritize tasks and allocate resources accordingly. Consider conducting a thorough needs assessment to identify specific requirements and constraints that will inform the development of your warehouse move checklist.
Timeline and Deadlines: Establishing a realistic timeline and setting clear deadlines for key milestones is crucial for effective planning and execution. Consider factors such as lease expiration dates, peak business seasons, and lead times for equipment procurement and installation when determining your relocation timeline. Allow sufficient time for each phase of the move, including planning, preparation, execution, and post-relocation activities, to minimize delays and ensure a smooth transition.
Budget and Resource Allocation: Determine the budget available for the warehouse relocation and allocate resources accordingly. Consider costs associated with leasing or purchasing a new facility, transportation logistics, equipment purchases or rentals, labor expenses, and other relocation-related expenses. Identify areas where cost-saving measures can be implemented without compromising the quality or safety of the move, such as optimizing transportation routes or negotiating favorable terms with service providers.
Regulatory Compliance and Permits: Ensure compliance with all applicable regulations and obtain necessary permits and approvals before initiating the warehouse relocation process. This may include zoning regulations, building codes, environmental permits, and occupational health and safety requirements. Engage with regulatory authorities and consult with legal and compliance experts to address any regulatory concerns and avoid potential legal liabilities or penalties.
Communication and Stakeholder Engagement: Effective communication and stakeholder engagement are critical for a successful warehouse relocation. Identify key stakeholders, including employees, suppliers, customers, landlords, and regulatory authorities, and develop a communication plan to keep them informed and engaged throughout the relocation process. Establish regular channels of communication, such as email updates, meetings, and progress reports, to address concerns, solicit feedback, and manage expectations effectively.
Risk Assessment and Contingency Planning: Conduct a thorough risk assessment to identify potential risks and vulnerabilities that may arise during the relocation process. This may include risks such as equipment failure, transportation delays, adverse weather conditions, or unforeseen regulatory changes. Develop a contingency plan that outlines alternative courses of action and mitigation strategies to address potential risks and minimize their impact on the move.
As you embark on your own warehouse relocation endeavor, remember that every tip contributes to a harmonious relocation experience. The meticulous choreography of these steps ensures that the rhythm of your operations remains uninterrupted even amidst the change. Whether driven by growth, efficiency goals, or strategic realignment, the success of your warehouse relocation rests on your ability to apply these insights effectively.
Frequently Asked Questions
How to plan a warehouse relocation efficiently?
Planning a warehouse relocation involves assessing current operations, developing a detailed plan, evaluating potential locations, coordinating with stakeholders, budgeting resources, ensuring regulatory compliance, arranging logistics and transportation, implementing safety measures, packing and labeling efficiently, and testing critical systems. By addressing these aspects comprehensively, you can ensure a smooth transition to your new facility while minimizing disruptions to operations.
What is a typical warehouse relocation policy?
A typical warehouse relocation policy outlines the procedures and responsibilities for moving to a new facility. It includes steps for planning, budgeting, compliance, logistics, safety, and post-relocation activities. This policy ensures a smooth transition while minimizing disruptions and ensuring compliance with regulations.
About The Author