How to Configure and Measure Pallet Rack Components?
Storage is an essential aspect of any manufacturing as well as shipping setup for a product’s safety as well as traceability. To keep your manufactured products, parts, and equipment safe and neatly organized, it is essential to build a storage racking system in your warehouse or an area in your industrial unit. This ensures safety and efficiency and speeds up the production process.
While opting for custom industrial racks is the best option in terms of right fitment, configuring and measuring pallet rack components is key to getting it right. This post discusses various aspects of pallet rack components, standards dimensions, measurement and configuration of each component on the rack and more.
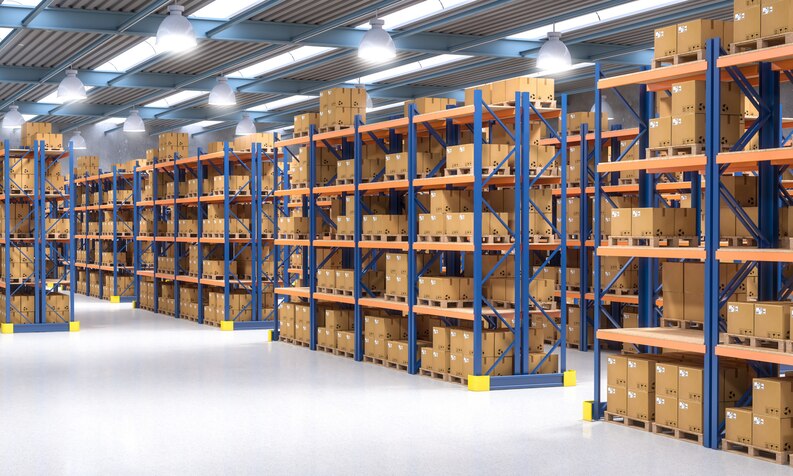
Overview of Common Pallet Racking Parts
Pallet racking systems are essential for efficient warehouse storage, and they consist of several key components:
Uprights (Frames): Uprights is one of the important pallet racking parts. These vertical structures form the framework of pallet racking systems. They support the horizontal beams and determine the overall height and depth of the shelving levels. Uprights are available in various sizes and configurations to accommodate different storage needs and load capacities.
Beams (Crossbars): Horizontal bars link to uprights and beams to form shelves for storing pallets or items. They are available in a variety of lengths and load capabilities to accommodate different pallet weights and sizes. Beams are frequently movable, allowing for various shelf arrangements.
Wire Mesh Decking: Wire mesh decking is placed on top of the beams to provide a stable surface for pallets. It is an important pallet racking part as it allows airflow and visibility, while also preventing items from falling through. Wire mesh decking enhances safety and reduces the risk of accidents in the warehouse.
Row Spacers: These metal bars or plates are placed between rows of pallet racking to ensure adequate spacing and stability. Row spacers guarantee that forklifts and other equipment may safely navigate between rows, reducing the danger of collisions and damage to the racking system.
Footplates: Footplates are metal plates fitted to the bottom of upright frames that equally distribute the system’s weight and anchor it to the floor. Proper anchoring is critical to the stability and safety of the racking system, particularly in high-traffic areas.
Bracing: Horizontal and diagonal bracing connect the uprights, adding strength and stability to the system. Bracing helps to distribute the load evenly over the structure and minimizes swaying or distortion, especially under high loads or seismic situations.
Safety Pins or Clips: These devices attach the beams to the uprights, preventing them from being dislodged and preserving the system’s safety and integrity. Safety pins or clips often have a locking mechanism that keeps the beams securely in place.
Anchors: Bolts or anchors are used to fasten the upright frames to the floor, providing additional stability and safety. These are one of the basic pallet racking parts. It helps prevent tipping or shifting, especially in areas prone to seismic activity.
End Protectors (Column Guards) and Row End Protectors: These protective barriers are attached to the ends of upright frames and rows of pallet racking, respectively. They help prevent damage from collisions with forklifts or other machinery, protecting both the racking system and the stored inventory.
Pallet Supports: Pallet support is also a one of important pallet racking parts. It installed between the front and rear beams of each shelf level, pallet supports provide additional support for pallets and help prevent sagging or bowing under heavy loads.
Frame Protectors: These guards are attached to the base of upright frames, protecting against damage from forklifts or other equipment. Frame protectors help extend the lifespan of the racking system by minimizing wear and tear on the uprights.
Labels and Signage: Tags or labels are affixed to components for inventory management, location identification, and safety instructions. Proper labeling and signage help improve organization, efficiency, and safety in the warehouse.
Pointers on Configuring and Measuring Pallet Rack Components and Frames
Here are some pointers that may be useful in constructing custom industrial racks and pallet frames to best suit your storage needs. These are applicable whether you want to repair or upgrade your existing storage racking system or build a new one from scratch.
- Determining storage requirements: Analyze the storage requirements in terms of the type of products or materials you need to store, their shape, size, weight, and so on. This will help you determine the space, shape, and weight bearing capacity you require for the racks.
- Measurement of available area: Measure the space available in terms of length, breadth, and depth. Identify the actual space available for building the pallet frame and the space left to move around.
- Configuration and measurement of the overall pallet rack system: A pallet rack system comprises upright frames and shelf beams connected to each other, wherein the dimensions and load bearing capacity are important aspects. Frames and beams have multiple tiers which store all the pallet loads. There are uprights that are formed by joining two columns with a series of horizontal and vertical struts. Baseplates are placed at the column base right up to the floor and hence serve as an anchor. When taking measurements, the front and rear columns must be considered separately as there may be slight variations. Each of these pallet rack components must be measured separately to get the right output.
- Measurement of upright frame dimensions: Here, you need to measure the upright frame depth, front and rear column depths, baseplate size, column height and width.
- Custom frame measurement: This depends on the number and types of custom frames you add to offer structural stability or meet specific application requirements. These frames usually do not cover the entire length of the main frame and are placed behind the front column. Measure their length from the floor to top end and depth from point zero to the welded point or joint for both front and rear columns.
- Beam measurement: Beams are horizontally placed supporting structures that connect to the uprights. Crossbeams have connectors at both ends that work as an interface between beams and uprights. You need to measure the beam length, thickness, and depth based on the pallet size. The beam dimensions need to be measured without considering the connector as a part of it. The beam length must be measured from the inner side of one upright to that of the opposite one. The beam thickness is an important aspect as it helps determine the load bearing capacity. The thicker the beam, the more is the capacity. This needs to be measured from top to bottom. The depth or width of the beam can be determined by measuring from front to the rear side.
- Beam connector plates: Beam connector plates secure the beam with the uprights as they are welded onto both ends of the crossbeam. Racks may either be roll-formed or have holes for connections. The roll-formed racks may have various types of connectors such as pins, clips, or bolts. Once you identify the types of beam connector, count the number of holes and measure the connector height, width, and depth. Also, measure the distance between each hole on the upright considering the center point of each hole as the beginning and end.
- Beam punches: Some beams may have punches at regular intervals. Based on the number of these punched holes, measure the beam edge and top to the center point of the punch hole. Repeat this for all the punches.
- Strut measurement: Struts are metal bar-like components placed horizontally or diagonally within the rack. Most struts are tubular; however, some may be square shaped. Measure the strut from the inner side from the floor to its connecting point with the column.
Step-by-Step Guide to Configuring Parts of Pallet Racking
Configuring a pallet racking system involves several key steps to ensure proper setup and functionality.
Assess Storage Needs: Initially, assess what goods need to be stored as well as their specific storage requirements such as size, weight and accessibility needs in order to choose an apt racking system configuration.
Measure Available Space: Use precise measurements of your warehouse or storage area’s dimensions and ceiling height to accurately ascertain available floorspace and ceiling height, so as to select and configure upright frames and beams of appropriate sizes and configuration. This data can help inform decision making.
Select Uprights and Beams: Based on an evaluation of storage needs and available space, choose upright frames and beams based on load capacity, beam length, upright height compatibility as well as load bearing capacities to meet those of goods to be stored.
Layout Design: Begin designing the pallet racking system’s layout design by considering factors like aisle width, row spacing, and number of shelving levels required. Either use software tools or sketch your configuration on paper for this step.
Position Uprights: Place the upright frames according to your layout design, using a level to ensure they are installed upright and plumb – this ensures a stable base for the rack system.
Attach Footplates: When attaching footplates to each upright frame, use anchors or bolts to fasten them securely to the floor using anchor points or bolts and ensure their proper anchorage using anchoring tools. Proper anchorage ensures stability and safety when operating in high traffic environments such as warehouses.
Install Beams: Secure horizontal beams onto upright frames at each shelving level in accordance to their height requirements, using safety pins or clips as anchor points and to avoid accidental dislodging of beams from their positions.
Add Wire Mesh Decking: For added support of pallets or goods, place wire mesh decking over beams in order to form stable shelves for them. Be sure that it’s properly aligned and secured against movement.
Install Bracing: Install horizontal and diagonal bracing between upright frames to reinforce their structure and enhance stability, following manufacturer specifications to secure them securely into place with hardware provided by them.
Add Accessories: Based on your individual requirements, accessories like row spacers, end protectors, pallet supports or frame protectors may help enhance safety and functionality for increased functionality and protection.
Labeling and Signage: Each shelving level should be marked with tags or labels to identify its contents and location, along with any necessary signs pertaining to safety guidelines, weight capacities or aisle directions.
Troubleshooting Common Configuration of Racking Components
Troubleshooting common configuration issues with pallet racking components is crucial for maintaining safety and maximizing storage efficiency in a warehouse. Here’s a guide to troubleshooting some common issues:
Uneven Shelving Levels: If shelving levels are uneven, check the alignment of the beams and uprights. Ensure that beams are properly seated in the connectors on the uprights and that all safety pins or clips are engaged. Adjust beam heights as needed to achieve level shelving.
Sagging or Bowing Beams: If beams are sagging or bowing under the weight of stored goods, consider upgrading to heavier-duty beams or adding additional support such as pallet supports or wire mesh decking. Verify that the beams are properly seated and secured to the uprights.
Instability or Swaying: If the racking system feels unstable or is swaying, check for missing or loose bracing. Ensure that horizontal and diagonal braces are properly installed and tightened according to manufacturer specifications. Consider adding additional bracing for reinforcement if necessary.
Floor Anchoring Issues: If upright frames are not securely anchored to the floor, the entire racking system may be at risk of tipping over. Check that footplates are properly aligned and anchored to the floor using appropriate bolts or anchors. Re-anchor any loose or unstable footplates to ensure stability.
Damage to Components: Inspect all racking components for signs of damage, such as bent beams, dented uprights, or broken connectors. Replace any damaged components immediately to prevent structural failure and ensure the safety of the racking system.
Misaligning Uprights: If the upright frames in question appear out-of-whack or leaning towards one direction, first make sure they’re securely fastened to the floor and all connections between uprights and beams are tight and secure. Use a level to check plumbness then make any necessary adjustments until alignment has been reached.
Overloading: Overfilling shelves with goods can place undue stress on their racking system and increase risk. Review load capacity guidelines for beams and uprights before redistributing or eliminating excess weight to avoid overloading.
Inadequate Clearance: Inadequate clearance between rows of rack can impede safe forklift and equipment movement, threatening safety. Be sure to adjust row spacers as necessary so there is enough clearance for maneuvering safely.
Improper Labeling and Signage: Poor shelf labeling or signage could create confusion and inefficiency within a warehouse environment, leading to frustration for employees as well as safety violations for staff members. Make sure shelves clearly display inventory information as well as any safety guidelines clearly displayed prominently for best performance in warehouse environments.
Regular Maintenance: Create and enforce a regular maintenance and inspection schedule in order to identify and address any potential problems promptly, such as loose bolts, damaged components or signs of wear and tear; this allows you to spot potential safety threats quickly before they escalate into serious safety risks.
Best Practices for Maintaining Warehouse Racking Parts
Maintaining warehouse racking parts is essential for ensuring the safety, longevity, and efficiency of the storage system. Here are some best practices for maintaining warehouse racking parts:
Regular Inspections: Implement a schedule for regular inspections of the racking system. Inspect all components, including upright frames, beams, bracing, footplates, and accessories, for signs of damage, wear, or misalignment.
Address Damage Promptly: If any damage is detected during inspections, address it promptly by repairing or replacing the damaged components. Do not ignore minor damage, as it can compromise the structural integrity of the racking system and pose safety risks.
Cleanliness: Keep the racking system clean and free of debris. Regularly remove dust, dirt, and other contaminants from shelves, beams, and uprights to prevent corrosion and maintain optimal performance.
Proper Loading Practices: Train warehouse staff on proper loading practices to avoid overloading shelves or placing heavy items unevenly. Ensure that loads are distributed evenly across beams and that weight capacities are not exceeded.
Secure Connections: Regularly check and tighten bolts, nuts, and connectors to ensure that all components are securely fastened. Loose connections can compromise the stability of the racking system and increase the risk of accidents.
Floor Anchoring: Verify that upright frames are securely anchored to the floor using appropriate bolts or anchors. Inspect footplates for stability and re-anchor any loose or unstable footplates as needed.
Bracing and Reinforcement: Check horizontal and diagonal bracing for signs of damage or looseness. Reinforce the bracing if necessary to maintain the structural stability of the racking system, especially in areas prone to seismic activity.
Labeling and Signage: Ensure that shelves are properly labeled with inventory information and safety guidelines. Clear and visible signage helps warehouse staff navigate the racking system safely and efficiently.
Training and Education: Provide training to warehouse staff on proper racking system maintenance and safety procedures. Educate them on how to recognize potential hazards and report any issues promptly.
Documentation and Record-Keeping: Maintain detailed records of inspections, repairs, and maintenance activities for the racking system. Keep track of any replacements or upgrades made to components and document any changes to the configuration of the system.
Professional Inspections: Consider hiring a professional racking system inspector to conduct periodic inspections and assessments of the system. Professional inspectors can identify potential issues that may not be apparent during routine inspections and provide recommendations for corrective actions.
The above information may offer some idea about the accurate ways to measure pallet rack components. However, in case you want to get it done in your storage unit, it is recommended to connect with an expert in this segment. Also, if you are looking for custom pallet racks for your application, ensure to source them from a reliable and certified player with experience in your industry segment. SPS Ideal Solutions specializes in the design and manufacturing of custom, racks, pallets, and more for shipping, storage, and shelving. You can contact their team via phone or email in case you are interested in sharing your requirements or have further questions in this segment.
About The Author