The Future of Industrial Storage: Advancements in Space Optimization
Industrial storage plays a pivotal role across diverse sectors, serving as the backbone of efficient operations and supply chain management. As businesses grapple with increasing demands for storage capacity and cost-effective solutions, the concept of space optimization emerges as a game-changer. Industrial space optimization focuses on maximizing the utilization of available space while maintaining accessibility and productivity.
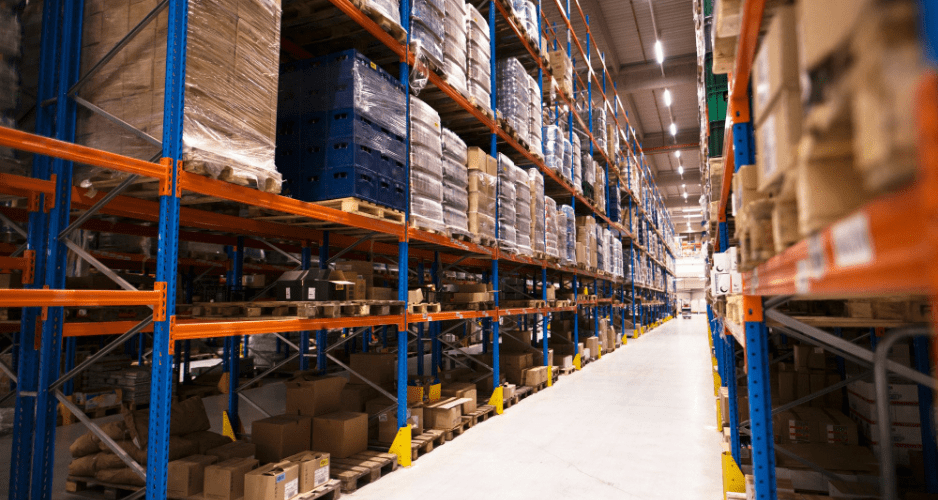
In this dynamic landscape, advancements and innovations are reshaping the future of industrial storage, introducing cutting-edge technologies and intelligent systems that redefine traditional storage methodologies. From high-density storage systems to AI-driven smart racking solutions, the future promises to revolutionize industrial storage practices, offering greater efficiency, sustainability and adaptability.
Current Challenges in Industrial Storage
Limitations of Traditional Storage Methods:
Traditional storage methods, such as static shelving or manual stacking, often come with inherent limitations that hinder optimal storage practices. These methods may not be well-suited for handling various types of inventory, leading to inefficiencies and potential damage to stored goods. Additionally, manual handling can be labor-intensive and time-consuming, impacting overall productivity and increasing the risk of errors or accidents.
Space Constraints on Operational Efficiency and Productivity:
With the growing demand for storage space and the rising cost of real estate, many industrial facilities face space constraints. Limited storage capacity can lead to overcrowded warehouses, cluttered aisles and difficulty in accessing inventory, resulting in reduced operational efficiency. Inefficient space utilization may also require excessive travel time for employees to retrieve items, leading to longer lead times and decreased productivity.
Cost Implications of Inefficient Storage Practices:
Inefficient storage practices can lead to higher operational costs for businesses. Over-utilization of floor space, lack of proper organization and inadequate inventory management can result in excess inventory carrying costs and increased labor expenses. Moreover, improper storage may lead to damaged or expired goods, causing financial losses and potential wastage.
Space Optimization in Industrial Storage
Utilizing Vertical Space:
Metals industry are embracing the concept of utilizing vertical space to maximize storage capacity. Vertical storage solutions, such as high-rise shelving systems, automated vertical carousels, and vertical lift modules, enable businesses to store items vertically, making efficient use of overhead space.
Automated and Robotic Storage Systems:
Automated storage and retrieval systems (AS/RS) use robotics and conveyors to efficiently move and retrieve inventory. These systems can handle heavy loads and execute storage and retrieval tasks with remarkable speed and precision. By eliminating manual handling, automated storage systems optimize operational efficiency, reduce labor costs and minimize the risk of errors in inventory management.
Modular and Customizable Storage Options:
Modular and customizable storage solutions offer businesses the ability to design storage layouts tailored to their specific requirements. These systems consist of interchangeable components, allowing for easy reconfiguration or expansion as the storage needs change. With modular storage, companies can optimize space utilization and create efficient workflows that accommodate diverse product types and inventory volumes.
Utilizing AI and Data Analytics:
AI-powered storage systems can analyze historical data, predict inventory demand and optimize storage locations based on usage patterns. This intelligence allows for dynamic inventory allocation, ensuring fast-moving items are strategically placed for easy access, while slower-moving items are stored in less accessible areas.
Advancements in Storage Technologies
High-density storage systems: High-density storage systems can utilize vertical space efficiently, allowing items to be stacked closer together and increasing storage density. By maximizing storage capacity, businesses can store more items in the same footprint, reducing the need for additional warehouse space. High-density storage systems, such as vertical carousels, automated storage and retrieval systems (AS/RS) and compact mobile shelving, provide easy access to stored items, enhancing productivity and operational efficiency.
Augmented reality (AR) and virtual reality (VR): Through AR and VR technologies, businesses can visualize and plan their warehouse layouts virtually, enabling them to experiment with different configurations before implementing changes physically. This innovation allows companies to optimize storage layouts, streamline workflows, and reduce the risk of errors during warehouse design.
Integration of Internet of Things (IoT) in storage systems: IoT sensors are incorporated into storage equipment and inventory to collect data on various parameters, such as temperature, humidity and usage patterns. This data is then transmitted and analyzed in real-time, providing valuable insights into storage conditions and inventory levels. With predictive maintenance capabilities, IoT-powered storage systems can detect potential issues before they escalate, minimizing downtime and optimizing maintenance schedules.
Smart racking systems with dynamic storage configurations: Smart racking systems are equipped with sophisticated technology that adjust their storage configurations based on inventory demand, optimizing space utilization and enhancing flexibility. Smart racking systems use automation and robotics to move shelves or racks to adapt to changing storage needs. By dynamically reconfiguring storage arrangements, smart racking systems can accommodate various product sizes, inventory volumes and seasonal demands efficiently.
Challenges & Considerations for Implementing Industrial Space Optimization
Initial Investment and ROI Analysis: Implementing space optimization in industrial storage may require a significant initial investment. High-density storage systems, advanced automation, and IoT integration can come with upfront costs. Businesses must carefully assess the return on investment (ROI) to justify the expenses. Conducting a thorough analysis of potential cost savings, increased storage capacity and operational efficiency gains is essential in determining the viability of space optimization solutions.
Training and Up skilling of Employees: Introducing new storage technologies and automation requires employees to be trained and up skilled to operate and manage these systems effectively. Training programs should cover the use of advanced equipment, IoT data interpretation and maintenance procedures. Proper training ensures that employees can adapt to the new storage methodologies, utilize the technology optimally and prevent potential operational challenges or errors.
Adapting to New Storage Methodologies: Implementing industrial space optimization often involves changes in workflow, storage layouts and job roles. Resistance to change can arise from employees who are accustomed to traditional storage practices. It is crucial for management to communicate the benefits of space optimization clearly, addressing any concerns and emphasizing how it will enhance efficiency and simplify processes. Encouraging an open dialogue and involving employees in the implementation process can foster a smoother transition to new storage methodologies.
It is imperative for businesses to wholeheartedly embrace the advancements in storage technologies. By adopting space-optimized storage solutions, companies can unlock a world of increased efficiency and enhanced sustainability. Embracing these innovations allows businesses to stay competitive in a rapidly evolving landscape, streamline their operations and make a positive impact on their bottom line. The future of industrial storage holds tremendous potential and those who seize it by embracing space optimization will undoubtedly lead the way towards a more efficient and sustainable future.
Why You Need Industrial Space Optimization
In today’s business environment optimizing space is not just a luxury but a vital necessity. Here’s why it matters;
Boosted Efficiency: By optimizing your space, you ensure that every inch of your facility is used efficiently. This helps in minimizing wasted space and streamlining workflows leading to improved efficiency.
Cost Savings: Inefficient use of space can drive up expenses such, as real estate costs inventory management expenses and labor costs. Through space optimization you can trim these costs. Enhance your financial performance.
Increased Productivity: Disorderly and chaotic spaces can hamper productivity by causing delays and making it hard for employees to find what they need. An organized layout enables access to resources promoting smoother operations and higher productivity levels.
Enhanced Safety: Crowded or poorly arranged spaces pose risks, to employee safety by raising the chances of accidents or injuries. Optimal space utilization and clear pathways contribute to creating a work environment for your staff.
Scalability: With business growth comes evolving storage requirements. An optimized layout allows for scalability enabling you to adjust to changing inventory demands and production needs without disruptions.
Competitive Advantage: In today’s fast-paced business environment, efficiency is key to staying competitive. By optimizing your industrial space, you can gain a competitive edge by delivering products faster, reducing costs, and improving overall customer satisfaction.
Sustainability: Optimal space utilization contributes to sustainability efforts by reducing the need for additional warehouse space and minimizing energy consumption. By adopting space optimization practices, you can make your operations more environmentally friendly.
5 Important Tips for Industrial Space Optimization
Optimizing industrial space requires careful planning and strategic implementation. Here are five essential tips to help you make the most of your space:
Conduct a Space Audit: Begin by assessing your current space utilization. Identify areas of inefficiency, such as underutilized spaces or congested aisles. A thorough space audit will provide valuable insights into where improvements can be made.
Implement Vertical Storage Solutions: Utilize vertical space to its fullest potential by investing in high-density storage solutions such as vertical shelving systems, mezzanines, or automated vertical carousels. These solutions allow you to store items vertically, freeing up floor space for other purposes.
Optimize Workflow Layouts: Design your facility layout to minimize travel distances and streamline workflows. Group related activities together and create clear pathways for employees and equipment. Consider implementing lean manufacturing principles to eliminate waste and improve efficiency.
Utilize Technology and Automation: Embrace technology and automation to optimize storage and retrieval processes. Automated storage and retrieval systems (AS/RS), IoT sensors, and warehouse management software can help you track inventory, optimize storage locations, and improve overall efficiency.
Invest in Employee Training and Engagement: Ensure that your employees are trained in space optimization techniques and actively involved in the process. Encourage them to identify opportunities for improvement and provide feedback on the effectiveness of implemented strategies. Engaged employees are more likely to support and sustain space optimization efforts.
Frequently Asked Questions About Industrial Space Optimization
What is the First Rule of Industrial Space Optimization?
The first rule of industrial space optimization is to conduct a thorough space audit. This involves assessing the current utilization of space within the industrial facility to identify areas of inefficiency and opportunities for improvement.
What Does Space Optimization Mean in Warehouse?
Space optimization in a warehouse refers to maximizing the use of available space while maintaining accessibility and productivity. It involves implementing strategies such as vertical storage solutions, workflow optimization, and technology integration to make efficient use of the warehouse space.
How to find Min. and Max. in Industrial Space Optimization?
Finding the minimum and maximum in industrial space optimization involves identifying the minimum amount of space required to store inventory efficiently and the maximum capacity of the available space. This can be determined through space audits, analysis of inventory volumes and types, and consideration of workflow and operational requirements.
About The Author